Industrial and Manufacturing
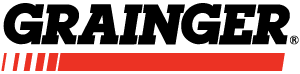
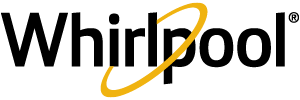
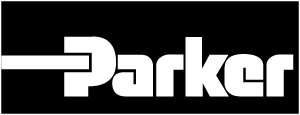
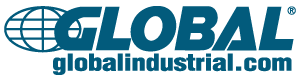
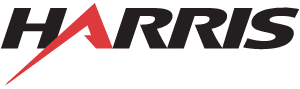
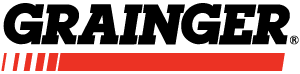
About W.W. Grainger
Grainger is a Fortune 500 company and is the leading supplier of maintenance, repair and operating products. With headquarters in Lake Forest, Illinois, they are home to over 22,000 employees. They sell over 1,200,000 different products, at 50,000 different locations, from 3,500 suppliers. Some of these products include electrical, vehicle maintenance, hardware, lighting, plumbing, safety, and test items.
What Clear Spider has Done
Clear Spider’s team of industry experts and software developers helped Grainger implement its VMI and CMI system for both internal and customer use. Through Clear Spider, Grainger is able to rapidly respond to the needs of hundreds of customers by having inside knowledge of what and how much they need restocked. Together with Clear Spider, Grainger streamlined their order process, set up automatic replenishment, optimized their system for user experience, implemented barcode technology, and much more.
Challenges
- Collaborative Inventory System
- Reliable Back-End and Flexible Front-End Inventory Systems
- Millions of SKUs and Thousands of Daily Transactions
- System Access Across Multiple Devices
Solutions
- Replenishment
- Fulfillment
- Barcode Scanning
- Vendor Managed Inventory
- Order Management
- Locally Hosted
- Batch Scanning
Results
- Increased Sales
- Improved Delivery Performance
- Reduced Stock-Outs by 10-25%
- Higher Service-Levels
- Closer Business Relationships
- Increased Information Transparency
- Shorter Lead-Times
Find out more in our detailed Grainger case study!
Learn more here.
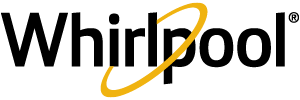
About Whirpool Corporation
The Whirlpool Corporation is an American multinational manufacturer and marketer of home appliances, headquartered in Benton Charter Township, Michigan. Globally known for their manufacturing and technological expertise, Whirlpool has solidified itself as a Fortune 500 company with over 70 production and research centers located around the world.
What Clear Spider has Done
Whirlpool chose Clear Spider to help with managing the Whirlpool Display division’s inventory and to provide a better solution for its order fulfillment process.
The Clear Spider team set up a special portal that Whirlpool Display’s dependants could access to see available products and match up the correct display to the model in question. The site features a host of features including order authentication by an administrator who can confirm the order is correct for the customer’s product. Finally, when orders are processed, Clear Spider creates a purchase order and invoice so the order can be checked for accuracy once again.
Clear Spider helps Whirlpool Displays obtain product requests and ship orders efficiently so they can continue to be a world leader in their industry.
Challenges
- Shipping and Receiving Accuracy
- Autonomous Stock Orders
- Inventory Data Reports
Solutions
- Custom Web Portal
- Custom Inventory Reports
- Order Authorization
- Min / Max Level Notifications
- Inventory Management with Serialization
Results
- Shorter and Streamlined Ordering Process
- Order Tracking
- Custom Reports and Better Internal Analysis
- Greater Order Accuracy
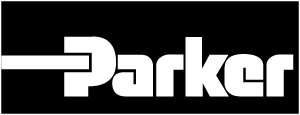
About Parker Hannifin
Parker Hannifin is a Fortune 250 company and a world leader in researching and producing motion and control technologies. Headquartered in Mayfield Heights, Ohio, Parker has over 100 years of experience developing hydraulics, pneumatics, electromechanical, filtration, process control, fluid and gas handling, sealing and shielding, climate control and aerospace technologies.
What Clear Spider has Done
Parker Hannifin wanted Clear Spider to be implemented in two different capacities – one for internal processes and one for their Vendor Managed Inventory operation.
Parker uses Clear Spider’s mobile app at their warehouse and in their customers’ distribution centers, as the main scanning tool for inbound inventory, outbound orders and cycle counts. The mobile app assists with keeping inventory accurate at Parker’s rural locations where network connections can be unreliable. The Clear Spider system also integrates with parts of Parker’s legacy software to streamline inventory data collection and create specialized inventory reports.
Clear Spider consolidates Parker Hannifin’s operations into a single, powerful, mobile system so they can meet the needs of their customers, more quickly and efficiently.
Challenges
- Inventory Level Data at Customers’ Warehouses
- In-Depth Inventory Reports
- Inventory System for Customers’ Warehouses
Solutions
- Integrations with Legacy Software
- Vendor Managed Inventory
- Barcoding
- Mobile App
- Min / Max Level Notifications
- Replenishment
- Cycle Counting
Results
- Integrations with Existing Software
- Comprehensive Inventory Data Reports
- Mobile Scanning and Data Upload
- Total Inventory Visibility
- Auto-Restocking Function
- Improved Customer Relationships
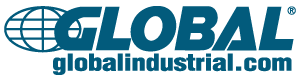
About Global Industrial
Global Industrial is a Fortune 1000 company that specializes in industrial and business supplies. Headquartered in Port Washington, New York, Global Industrial carries over 1,000,000 products for organizations ranging from Fortune 500 companies and government institutions to small businesses and agencies.
What Clear Spider has Done
Clear Spider was brought in to assist Global Industrial with a system that could be used both internally and at their customers’ locations.
Clear Spider was deployed at both Global Industrial’s warehouses and their customer locations as part of their VMI program. The cloud-based solution allows Global Industrial’s customers to actively track their own inventory while easily ordering more via a seamless ordering process. This relationship helps to keep the customers’ locations fully stocked and the recurring replenishment keeps products flowing through Global’s own warehouses. Additionally, Global Industrial can gather inventory data on outbound orders to identify trends and forecast future demand.
Through the implementation of Clear Spider, Global Industrial and their customers can enjoy a more streamlined inventory system with increased operational efficiencies and functionality.
Challenges
- System Available to Customers
- Slow Reaction to Customer Needs
- Customer Demands and Trend Forecast
Solutions
- CMI/VMI Capabilities
- Replenishment Function
- Cloud Based Software
- Distribution, Shipping and Receiving
- Min / Max Levels and Notifications
Results
- Automatic Data Gathering and Analysis
- Customer Order Management
- Greater Inventory Turnover
- Visibility into Customer’s Needs
- Reduced Customer Stock-Outs
- Faster Reaction to Customer Demands
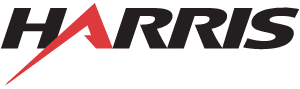
About Harris Products Group
The Harris Products Group is a world leader in metal-working products used in industries such brazing, welding, cutting, soldering and gas distribution. Headquartered out of Mason, Ohio, Harris currently operates manufacturing facilities in Mason, Ohio, USA; Gainesville, Georgia, USA, Dzierzonow, Poland, and Sao Paulo, Brazil.
What Clear Spider has Done
The primary reason Harris Products Group chose Clear Spider to manage its inventory was the robust solution Clear Spider was able to provide.
One of Clear Spider’s main functions is to act as gateway between Harris’s customers’ ERP systems and Harris’s own internal system. The primary function is to feed current inventory status and item planning parameters from their customers’ systems to Clear Spider on a regularly scheduled basis. Once the items in Clear Spider are updated, the replan function is run to generate replenishment orders for the various customer sites. When these replenishment orders are acknowledged, a purchase order is generated and transmitted to Harris’s system where the order is fulfilled.
Using Clear Spider, Harris can focus on developing quality products and can have peace of mind knowing exactly what their customers need more of and when they need it by.
Challenges
- Variety of Diverse Customers
- Integration with Several ERP Systems
- Minimal Inventory Visibility
Solutions
- Vendor Managed Inventory
- Integrations (EDI, SAP)
- Replenishment Function
- Replan Function
- Fulfillment
Results
- Quicker Reaction to Customer Needs
- Visibility into Customers’ Inventories
- Automatically Receive and Process Data from ERP Systems
- Automatic Purchase Order Creation and Fulfillment